As a core component of magnetrons, our copper anode works synergistically with the cathode to create the interaction space for electrons and high-frequency electromagnetic fields. Engineered to operate under constant magnetic and electric fields, it ensures efficient energy conversion while precisely controlling oscillation frequencies—surpassing conventional diode anodes in both functionality and precision.
2. Advanced Material Processing for 2.0mm Oxygen-Free Copper
Material Excellence: Fabricated from high-purity oxygen-free copper (C10100/C10200) with a thickness of 2.0mm, optimized for thermal and electrical conductivity.
Flawless Edge Quality: Laser-cut edges maintain a polished, burr-free surface (Ra ≤ 0.8μm), with sharp corner tolerances controlled within 0.5mm to prevent field distortion.
3. Micron-Level Precision Machining
Ultra-Tight Tolerances: Total length accuracy held to ±0.005mm, with other critical dimensions maintained within ±0.01mm.
Geometry Stability: CNC stamping and EDM (electrical discharge machining) ensure dimensional consistency across mass production batches, critical for resonant cavity performance.
4. Industry-Leading Quality Assurance
Automated Optical Inspection (AOI): 100% in-line measurement to verify compliance with aerospace-grade specifications.
Stress Relief Treatment: Vacuum annealing eliminates internal stresses, enhancing durability under high-power cyclic loads.
Products details
Precision Cut Anode Technology for Magnetrons
Critical Role in Energy Conversion
Manufacturer of Precision Cut Anode anodes for magnetrons with ±0.005mm tolerance. Oxygen-free copper (2.0mm) with laser-cut edges (Ra ≤ 0.8μm).
Precision copper anodes serve as core components in magnetrons, creating the interaction space for:
-
Electron movement control
-
High-frequency electromagnetic field generation
-
Efficient energy conversion (surpassing conventional diode anodes)
Advanced Material Specifications Oxygen-Free Copper Excellence
-
Material Grade: C10100/C10200 (2.0mm thickness)
-
Key Properties:
-
Thermal conductivity: ≥ 398 W/(m·K)
-
Electrical conductivity: ≥ 101% IACS
-
Purity: 99.99% Cu
-
Surface Perfection
-
Laser-cut edge quality: Ra ≤ 0.8μm
-
Corner tolerance: ≤ 0.5mm (prevents field distortion)
Micron-Level Manufacturing Process
Precision Machining Technologies
-
CNC Stamping
-
Batch consistency for mass production
-
-
Electrical Discharge Machining (EDM)
-
Complex geometries with ±0.01mm accuracy
-
Tolerance Standards
Dimension | Tolerance |
---|---|
Total Length | ±0.005mm |
Critical Features | ±0.01mm |
Angular Alignment | ±0.05° |
Quality Assurance Protocol
Inspection Methods
✔ Automated Optical Inspection (AOI)
✔ Coordinate Measuring Machine (CMM)
✔ Eddy Current Testing
Post-Processing
-
Vacuum annealing: Stress relief
-
Surface passivation: Oxidation resistance
Learn more about Zhengqiang’s strength
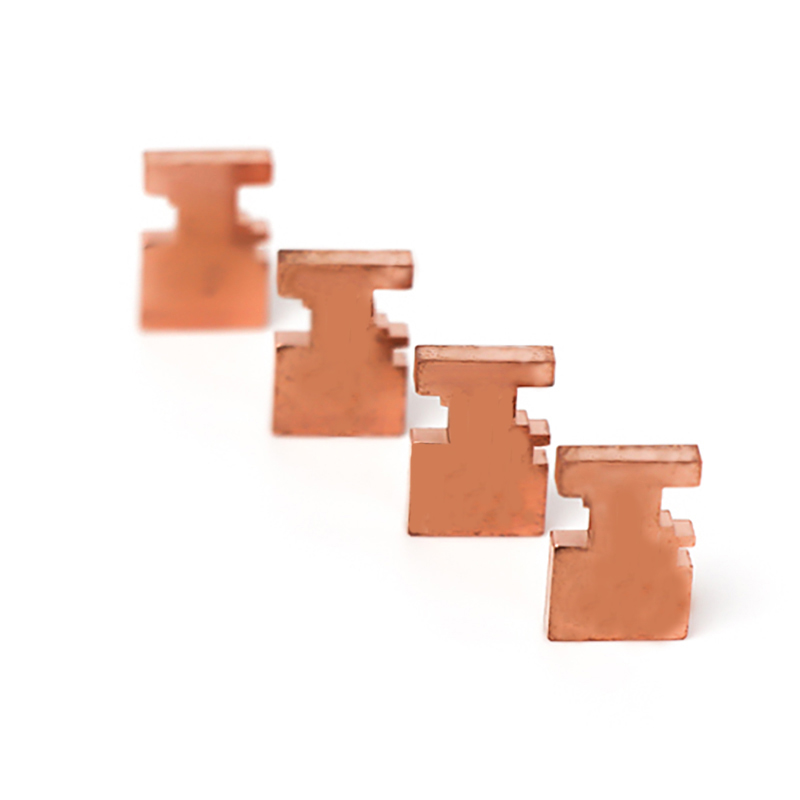
1. Critical Role in Magnetron Energy Conversion As a core component of magnetrons, our copper anode works synergistically with the cathode to create the interaction space for electrons and high-frequency electromagnetic fields. Engineered to operate under constant magnetic and electric fields, it ensures efficient energy conversion while precisely controlling oscillation frequencies—surpassing conventional diode anodes in both functionality and precision.
2. Advanced Material Processing for 2.0mm Oxygen-Free Copper Material Excellence: Fabricated from high-purity oxygen-free copper (C10100/C10200) with a thickness of 2.0mm, optimized for thermal and electrical conductivity. Flawless Edge Quality: Laser-cut edges maintain a polished, burr-free surface (Ra ≤ 0.8μm), with sharp corner tolerances controlled within 0.5mm to prevent field distortion.
3. Micron-Level Precision Machining Ultra-Tight Tolerances: Total length accuracy held to ±0.005mm, with other critical dimensions maintained within ±0.01mm. Geometry Stability: CNC stamping and EDM (electrical discharge machining) ensure dimensional consistency across mass production batches, critical for resonant cavity performance.
4. Industry-Leading Quality Assurance Automated Optical Inspection (AOI): 100% in-line measurement to verify compliance with aerospace-grade specifications. Stress Relief Treatment: Vacuum annealing eliminates internal stresses, enhancing durability under high-power cyclic loads.
FAQ: Precision Cut Anodes for Magnetrons
Q1: What makes your precision cut anodes superior for magnetron applications?
A: Our anodes combine three critical advantages:
-
Material purity – 99.99% oxygen-free copper (C10100/C10200)
-
Ultra-tight tolerances – ±0.005mm length accuracy
-
Surface perfection – Laser-cut edges with Ra ≤ 0.8μm roughness
Q2: How do you ensure dimensional stability in mass production?
A: Through our proprietary process control:
-
CNC stamping with real-time force monitoring
-
EDM finishing for critical features
-
100% automated optical inspection (AOI)
Q3: What’s your maximum production capacity for these precision anodes?
A: Current capacity highlights:
-
Prototype phase: 50-100 pcs/week
-
Mass production: 10,000+ pcs/month
-
Lead time: 2 weeks (standard), 4 weeks (custom)
Q4: Can you provide anodes for other high-frequency applications beyond magnetrons?
A: Yes, our technology adapts to:
-
Klystrons
-
RF amplifiers
-
Particle accelerator components
Q5: What quality certifications do your anodes comply with?
A: Our full certification suite includes:
✔ ISO 9001:2015
✔ AS9100D (Aerospace)
✔ RoHS/REACH compliance
✔ MIL-STD-883 (Method 2010.8)