Types of Custom Stamping Dies
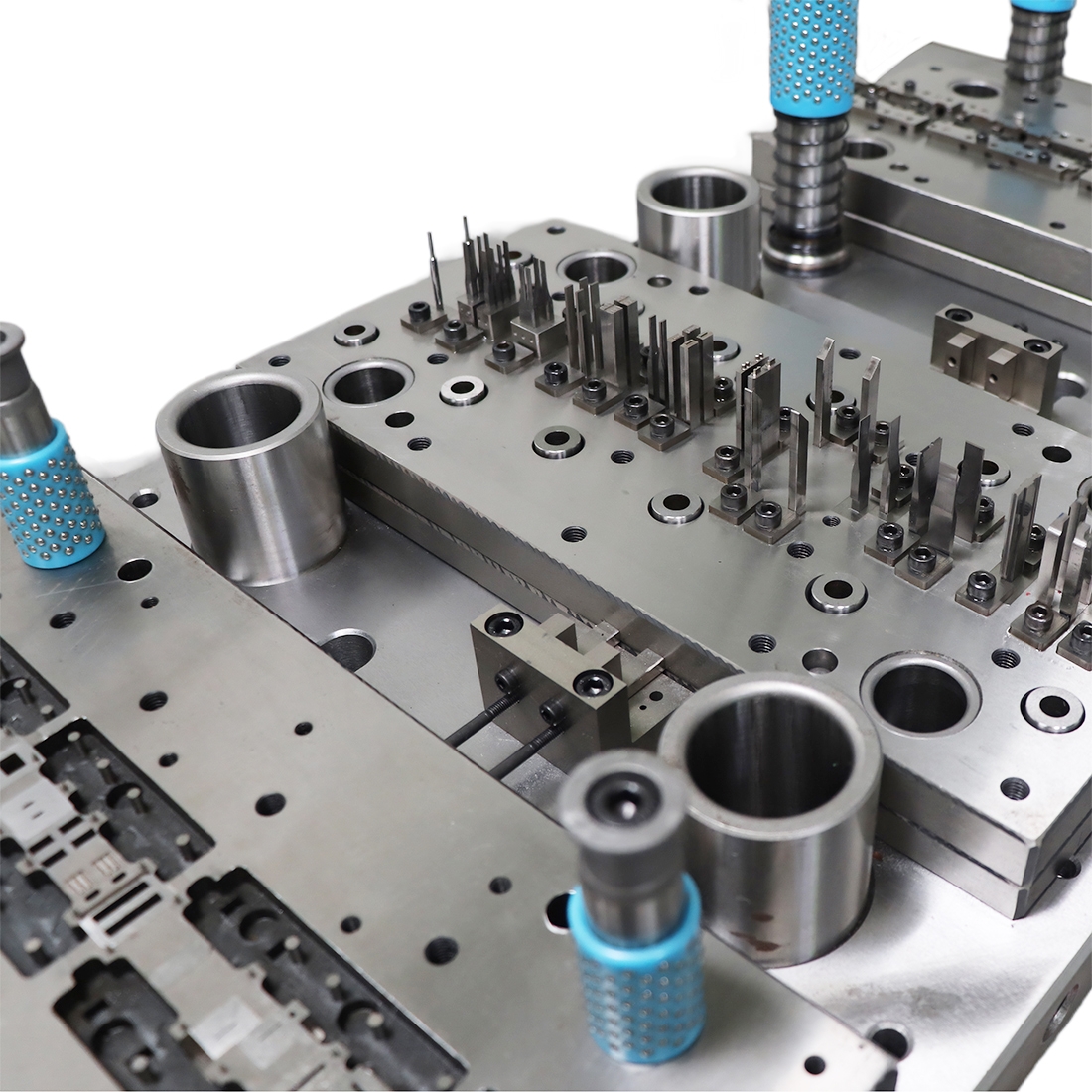
High-precision thick-cut stamping and stretching parts continuous die
Applicable to the shell components of automobile engines. Use stretching, cutting, punching and other multi-effect integrated processes to make some products basic molding. Applicable to a variety of metal materials and thicker products.
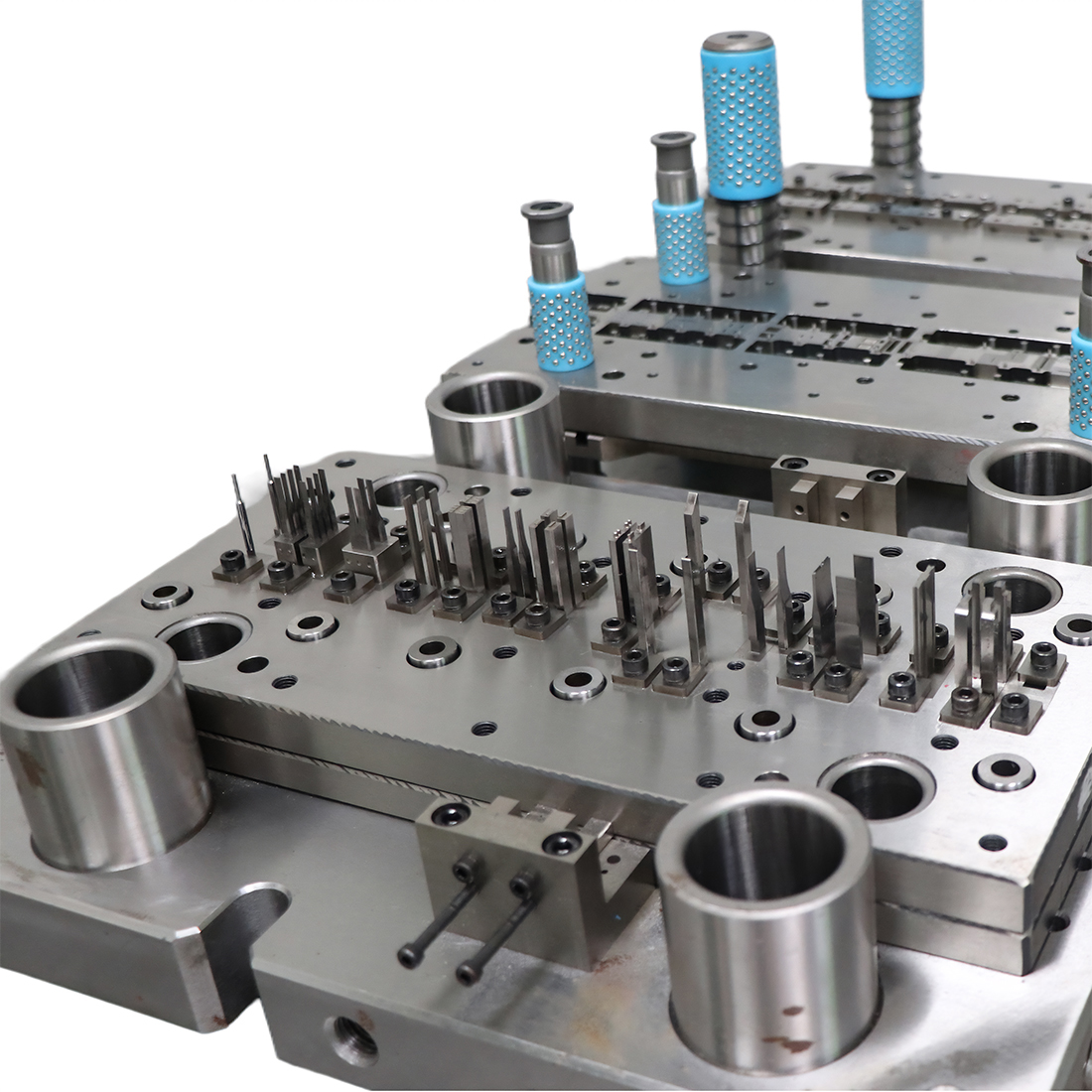
High-speed high-precision bending hardware continuous die
Applicable to the production of various connector ports and internal precision hardware parts. It is generally used to use carrier finished products and is suitable for the manufacture of connectors such as iron shells.
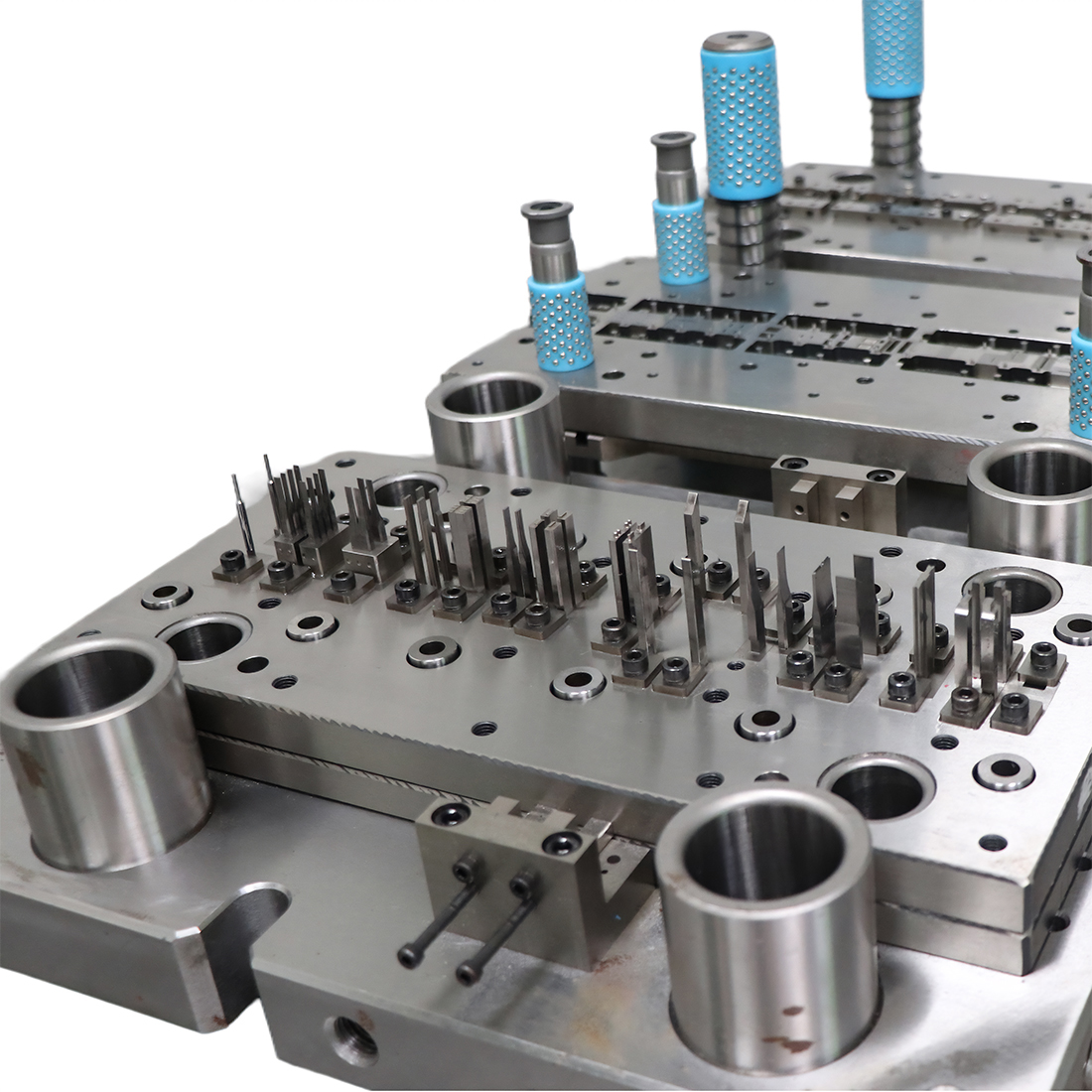
High-speed high-precision bending hardware continuous die
Applicable to the production of various connector ports and internal precision hardware parts. It is generally used to use carrier finished products and is suitable for the manufacture of connectors such as iron shells.
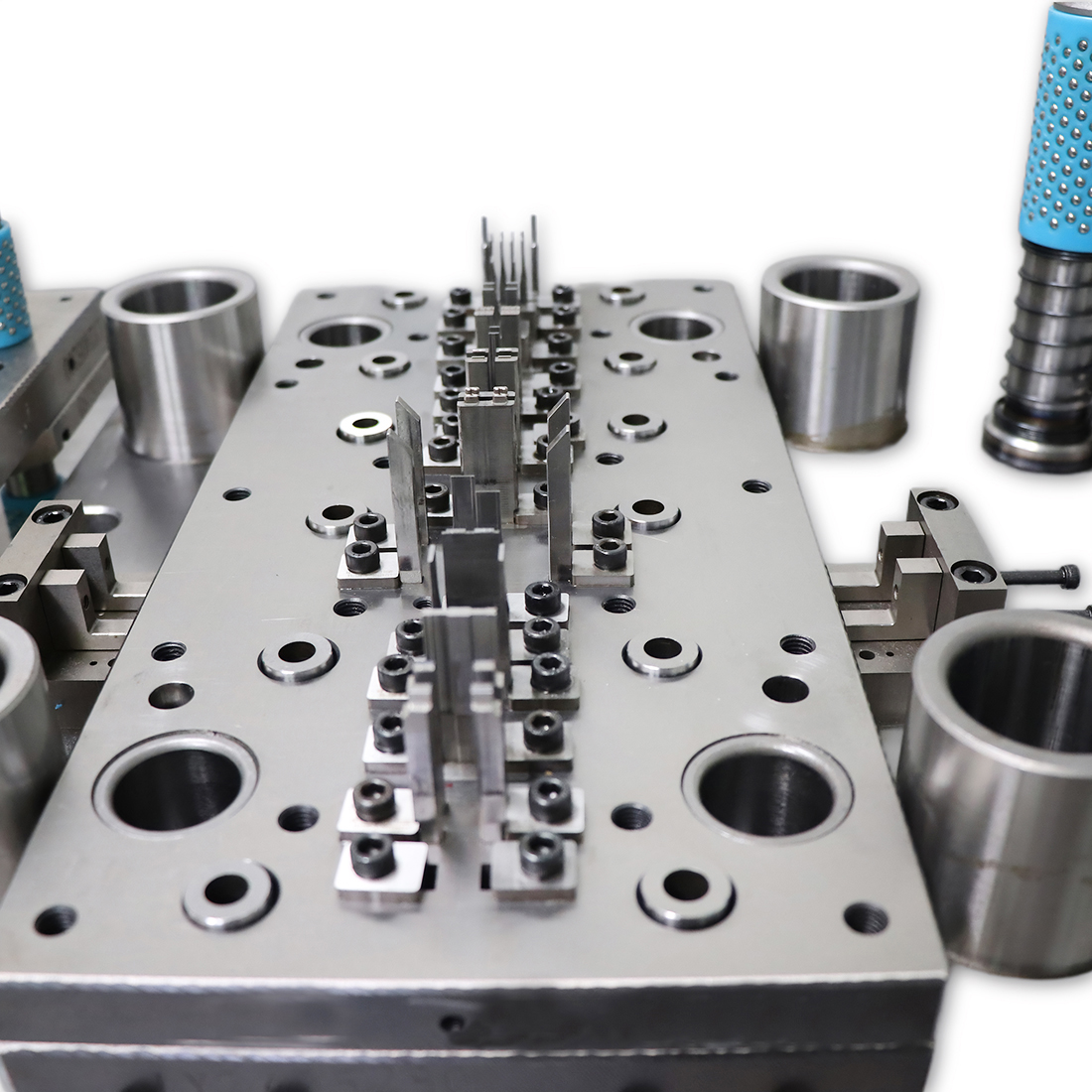
Progressive die for stretching, bending and punching hardware
Applicable to any hardware parts with multiple processes such as stretching, punching, cutting, bending, flanging, etc., and use the mold for one-time molding solutions for products with high surface requirements and high dimensional difficulty.
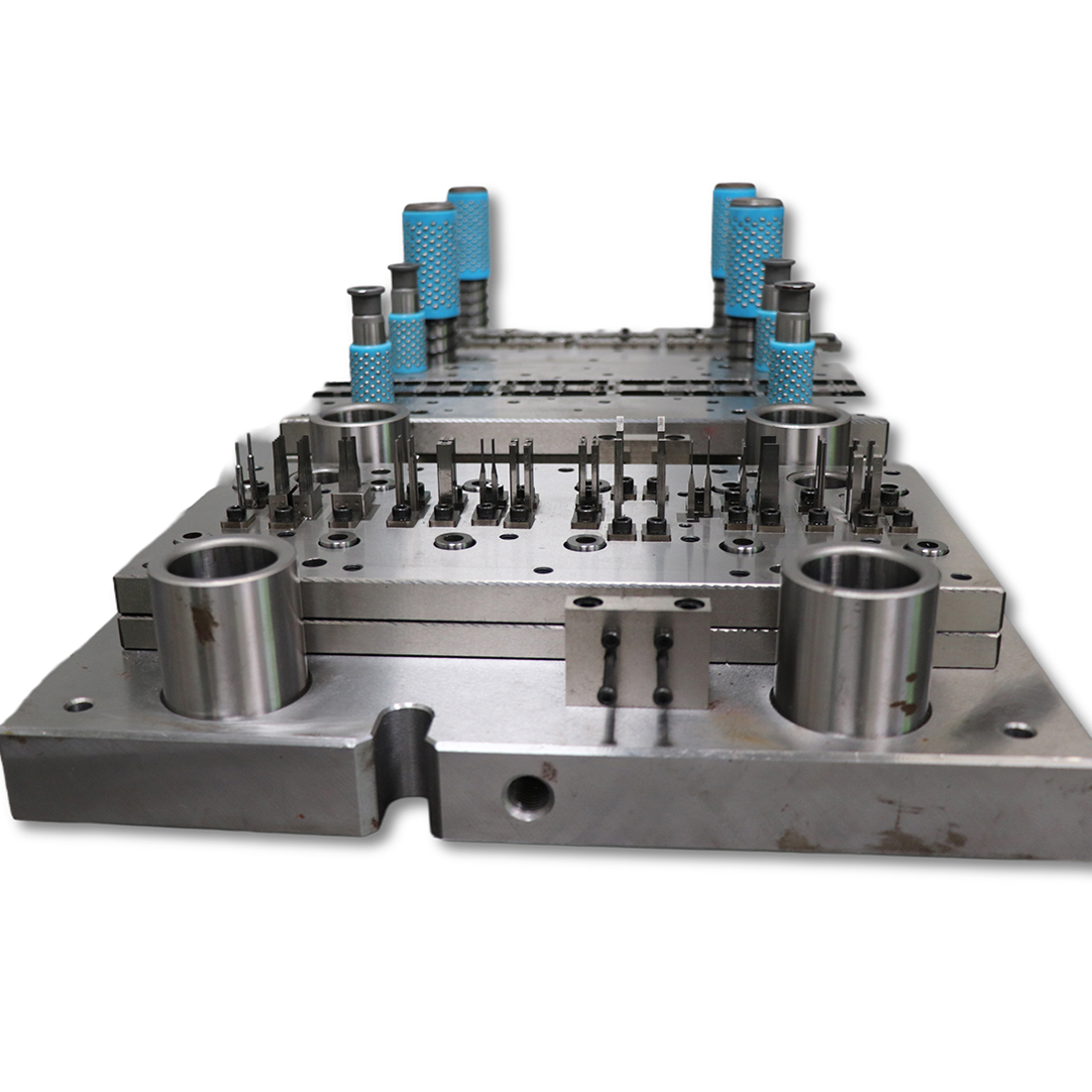
Continuous molding die for punching and bending parts
Applicable to any hardware parts with multiple processes such as stretching, punching, cutting, bending, flanging, etc., and use the mold for one-time molding solutions for products with high surface requirements and high dimensional difficulty.
Technical Advantages of Zhengqiang's Custom Stamping Dies
Zhengqiang Group is a high-tech enterprise specializing in the design and manufacturing of metal stamping molds. Guided by the core philosophy of “Do It Right the First Time,” we are committed to providing customers with high-precision, high-efficiency mold solutions. With years of industry expertise, we serve diverse sectors including automotive manufacturing, consumer electronics, new energy, medical devices, and aerospace. Equipped with advanced technology, rigorous quality control systems, and full-cycle service support, we have become a trusted partner in global industrial manufacturing.
High precision ±0.01mm
Using CAD/CAE software, CNC discharge machining, and slow wire technology, the mold cavity accuracy is ±0.01mm, which is suitable for high-precision requirements such as electronic connectors, automotive stamping parts, and medical parts.
30% efficiency improvement
Provide customized solutions for automated molds such as multi-station progressive dies and compound molds, which can integrate multiple processes such as stamping, stretching, and forming to achieve high-speed continuous production. Effectively shorten the production cycle and reduce labor costs.
Material utilization rate reaches 90%+
AI intelligent pattern arrangement system optimizes material layout and reduces waste. In the new energy battery shell project, the annual material cost savings exceed one million yuan.
Full life cycle service
Provide customized solutions for automated molds such as multi-station progressive dies and compound molds, which can integrate multiple processes such as stamping, stretching, and forming to achieve high-speed continuous production. Effectively shorten the production cycle and reduce labor costs.
Industry Applications
Zhengqiang is deeply engaged in the field of precision manufacturing. With advanced process technology and strict quality management, it widely serves multiple industries, including home appliances, consumer electronics, high-end kitchen appliances, new energy vehicles, medical instruments, industrial automation, etc. We provide customers with customized solutions to ensure that the products meet industry standards in terms of performance, precision and durability.

Automobile manufacturing
Applicable to thick plate parts such as engine housings, and one-time forming through multi-process composite molds to improve structural strength and processing efficiency.
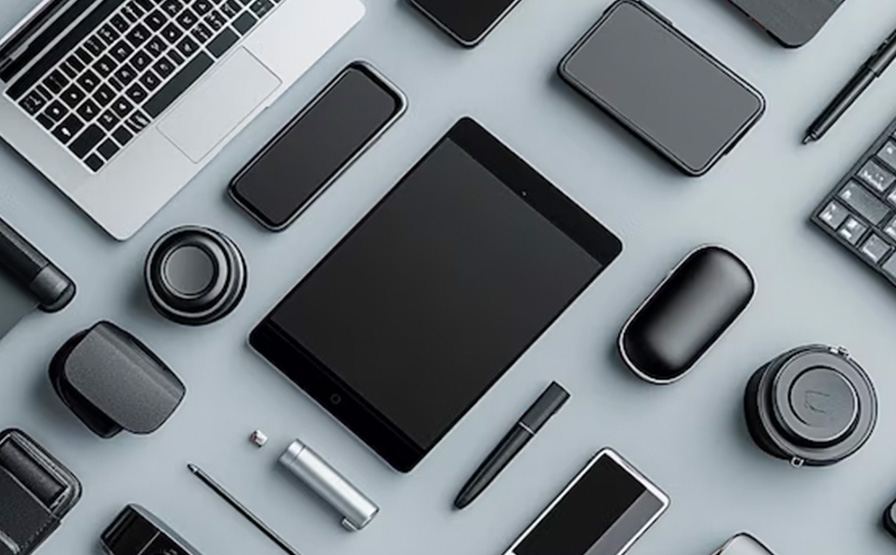
Electronic components
Applicable to tiny hardware such as USB terminals and precision connectors, and the carrier mold supports high-speed and high-consistency mass production.
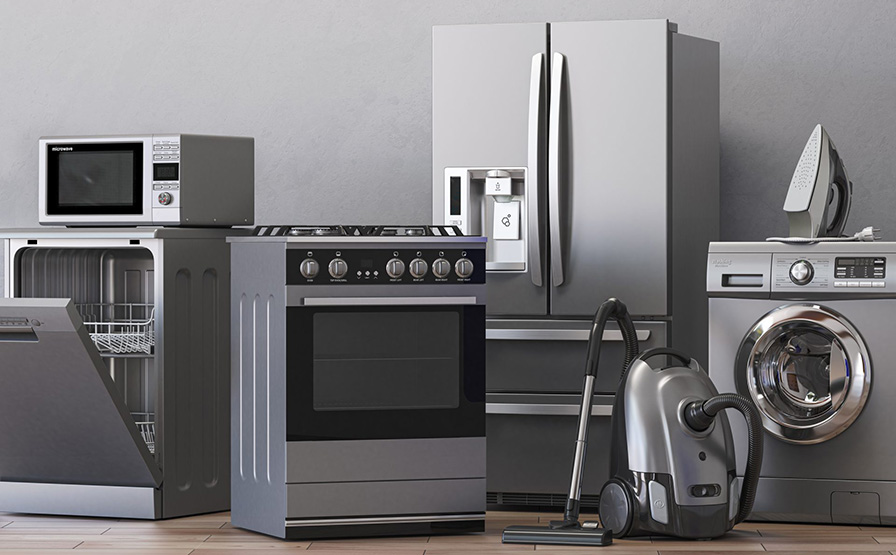
Home Appliances
Applicable to multi-process integrated components such as punching, bending, flanging, etc., to improve the yield rate and simplify the assembly process.
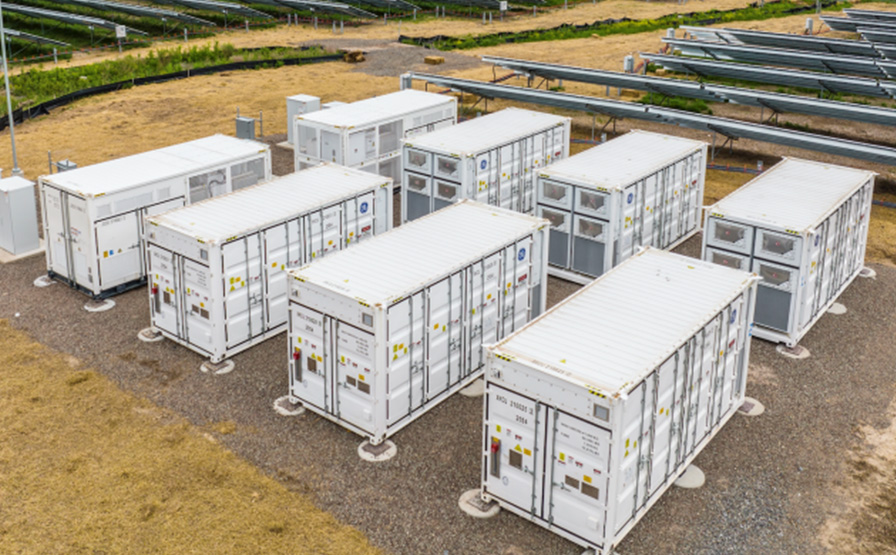
Photovoltaic energy storage
Adapt to structural parts such as power battery housing, combined with high-tonnage mold technology to ensure molding accuracy and material utilization.
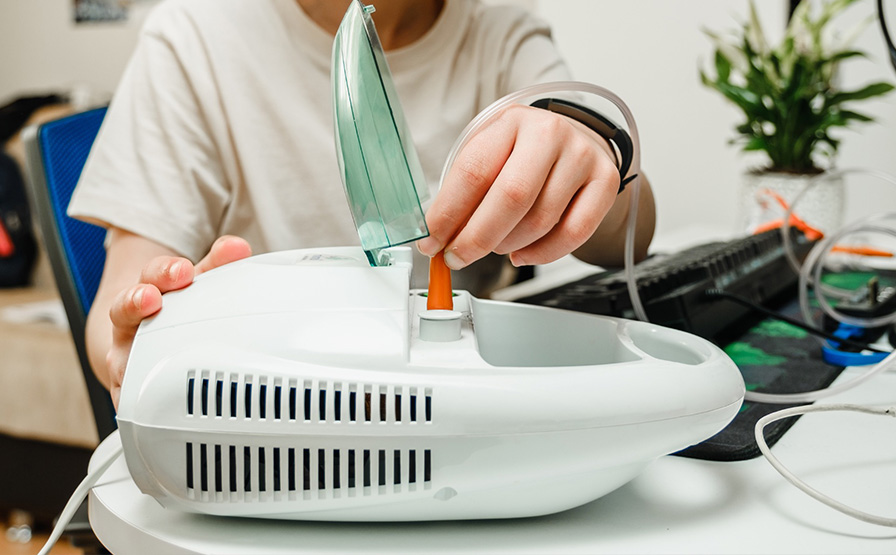
Healthcare & Medical Devices
Used for sensor brackets, housings and other parts, the mold meets the medical-grade accuracy and stability requirements.
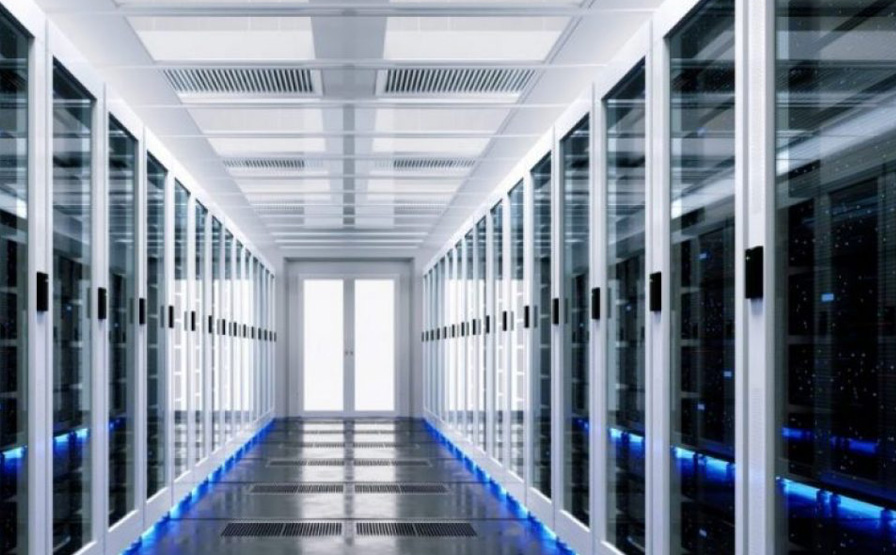
Communication equipment
Meet the high-precision stamping needs of thin metal shells and electromagnetic shielding parts, and adapt to the manufacturing of 5G equipment structural parts.
Precision Stamping Die Customization Process
Zhengqiang Mould adopts standardized and intelligent process flow, covering the whole process control from demand analysis to mass production delivery, ensuring high-precision, high-efficiency and low-cost production.
1. Demand analysis: from drawings to feasible manufacturing solutions
We conduct one-on-one technical docking with customers, gain an in-depth understanding of their product process requirements and application scenarios, and perform the following steps:
· Customer demand assessment: Confirmation of key parameters such as structure, output, precision, and budget
· Process feasibility analysis: Evaluate whether processes such as stamping or injection molding are feasible and avoid potential problems
· Cost accounting: Formulate reasonable quotations based on materials, processes, and quantities
2. Mold design: Accurate modeling and optimized structure
In the design stage, we use CAD modeling + CAE simulation + optimized structure to ensure that the mold is both efficient and durable:
· CAD three-dimensional modeling: Complete modeling mold structure
· CAE molding simulation analysis: Detect material flow, stress concentration and other problems
· Structural optimization: Weight reduction design, rib design, and improve overall performance
3. Processing and manufacturing: High-precision equipment creates high-quality mold cavities
We have a complete high-precision manufacturing production line to ensure mold molding accuracy and life:
· CNC precision machining: mold part size accuracy guarantee
· EDM electric spark molding: achieve complex mold cavity detail processing
· Heat treatment process: hardness increased to HRC58-62, wear-resistant and fatigue-resistant
4. Assembly and debugging: full inspection and verification, fast delivery
The experienced assembly team ensures mold assembly accuracy and quickly completes debugging:
· Mold assembly: all parts are docked according to the drawings with high precision
· Mold trial verification: use mass production equipment to test the mold, and fully inspect the dimensions
· Support mass production delivery: from small batch trial production to mass production molds with an annual output of millions of pieces
5. Quality control: quality assurance throughout the entire process
Zhengqiang implements a strict quality control system, equipped with 2.5-dimensional measuring instruments, cleanliness testing equipment and other precision instruments to achieve:
· Online process detection: real-time monitoring of key dimensions
· Full inspection/sampling before shipment: ensure zero defects in delivery
· Labels & protective packaging: meet export and long-distance transportation requirements
6. Shipping and after-sales: guaranteed delivery and worry-free service
We cooperate with many global logistics companies to provide flexible delivery methods and promise comprehensive technical support:
· On-time delivery: complete order delivery on schedule
· Global transportation solutions: meet the shipping needs of multiple regions
· After-sales service: remote technical guidance, product maintenance, quality tracking
Contact Us for Custom Stamping Die Solutions
Ready to enhance your production with precision stamping dies?
Contact our engineering team to discuss your project requirements and receive a customized solution.