Metal Stamping Mould Solutions
Metal stamping mould with ±0.01mm accuracy and 1.5M+ cycles. We deliver efficient, high-precision tools tailored to your industry.
Why Choose Zhengqiang for Your Metal Stamping Mould Needs?
Zhengqiang Group is a high-tech enterprise specializing in the design and manufacture of metal stamping dies. Adhering to the core concept of “doing things right the first time”, it is committed to providing customers with high-precision and high-efficiency die solutions. The company has been deeply involved in the industry for many years, and its service areas cover automobile manufacturing, consumer electronics, new energy, medical equipment, aerospace, etc. With advanced technical equipment, rigorous quality control system and full-process service support, it has become a reliable partner in the global industrial manufacturing field.
High-precision mold design
Use the internationally leading CAD/CAE design software to achieve accurate simulation and optimization of metal stamping mould structure and predict the risk of stamping deformation. Combining CNC electrospark machining (EDM) and slow wire cutting technology, ensure that the mold cavity accuracy is stable within ±0.01mm, and adapt to micron-level precision parts (such as electronic connectors, medical surgical instruments).
Efficient production and improved efficiency
Multi-station progressive die and compound die design: integrate multiple processes such as punching, stretching, and forming to achieve continuous automated production and reduce manual intervention. High-speed stamping equipment: equipped with 45 punching machines (25T-300T) and 8 multi-station high-speed punching machines, with a daily production capacity of over 100,000 pieces, supporting large-volume orders.
Material utilization optimization
AI intelligent layout system: optimizes the layout of the plate through algorithms, reduces corner waste, and achieves industry-leading material utilization (90%+). Continuous mold waste recycling design: accurately control the position of the waste belt to achieve secondary utilization of scraps.
Worry-free delivery of full life cycle services
From mold design and development, mold trial verification to mass production maintenance, we provide 24-hour technical response and regular maintenance services. Using SKD11/DC53 high-hardness alloy steel molds, combined with TD coating technology, the mold life exceeds 1.5 million times, reducing customers' downtime and mold change losses
What is a Metal Stamping Mould?
A metal stamping mould is a precision-engineered tool used to shape or cut sheet metal into specific forms without the application of heat. During the stamping process, a male punch forces the metal sheet into a female die that mirrors the desired shape. High-pressure stamping machines ensure the metal conforms exactly to the mould’s contours, delivering consistent and accurate results.
Metal stamping moulds are highly versatile and vary widely in size and geometry, making them suitable for a broad range of industries—from microelectronics to automotive and aerospace. Depending on the complexity of the project and the type of stamping required, several mould types are commonly used:
Progressive Dies
Progressive stamping uses metal stamping moulds that perform a series of cutting and bending operations in a continuous sequence. As the metal strip moves through each station, the component is gradually shaped—ideal for high-volume production with consistent geometry.
Transfer Dies
Unlike progressive dies, transfer dies work with individual metal blanks that are mechanically moved between stations. These metal stamping moulds are particularly suitable for larger or deep-drawn parts and are commonly used in applications where progressive dies are not feasible.
Line Dies
Line dies are used in tandem-line stamping, where large components undergo sequential operations across multiple presses. These metal stamping moulds are ideal for oversized parts that cannot be processed in a single die station.
Compound Dies
Compound dies perform cutting and shaping in one single stroke, significantly enhancing efficiency. These metal stamping moulds are best suited for parts that require both operations in a streamlined, cost-effective process.
Choosing the right metal stamping mould depends on your part’s geometry, production volume, and stamping method. An experienced supplier like Zhengqiang Group can help assess your requirements and recommend the optimal mould solution tailored to your project.
How Metal Stamping Mould Work
The basic principle of the working of metal stamping mould is to place the metal material in the working cavity of the die through the up and down movement of the die and the pressure of the punching machine, and use the stamping process to make the metal material subject to the requirements of the picture outline and size, so as to obtain the required stamping parts. The specific working principle is as follows:
1. Die installation: install the stamping mould on the punching machine, and realize the stamping action through the up and down movement of the mould.
2. Material placement: place the metal material to be processed in the working cavity of the die and fit it with the upper and lower parts of the die.
3. Die movement: the punching machine moves the die up and down through the mechanism and transmission device. When the die moves downward, the metal material is deformed by the stamping pressure.
4. Stamping of metal materials: when the die is pressed down into place, the punching machine applies pressure to make the die perform stamping processing on the metal material. Under the action of the stamping pressure, the metal material is impacted and deformed by the boss or groove on the inside of the die, so as to present the shape of the specified graphics and size.
5. Die return: after the stamping is completed, the die returns to the starting position through the mechanism and transmission device, ready for the next medium pressure.
Our Metal Stamping Mould Process
Zhengqiang Moulds adopts standardized and intelligent process flows, covering full-cycle control from demand analysis to mass production delivery, ensuring high precision, efficiency, and cost-effectiveness.
Process Steps | Key Activities |
Demand Analysis | Customer requirement evaluation → Process feasibility analysis → Cost estimation |
Mold Design | CAD modeling → CAE forming simulation → Structural optimization (weight reduction/enhancement) |
Machining & Manufacturing | CNC precision machining → EDM cavity forming → Heat treatment (hardness HRC58-62) |
Assembly & Debugging | Mold assembly → Trial testing (full dimensional inspection) → Mass production delivery (supports small to million-unit orders) |
Advanced Stamping Mould Design for High-Precision and Efficiency
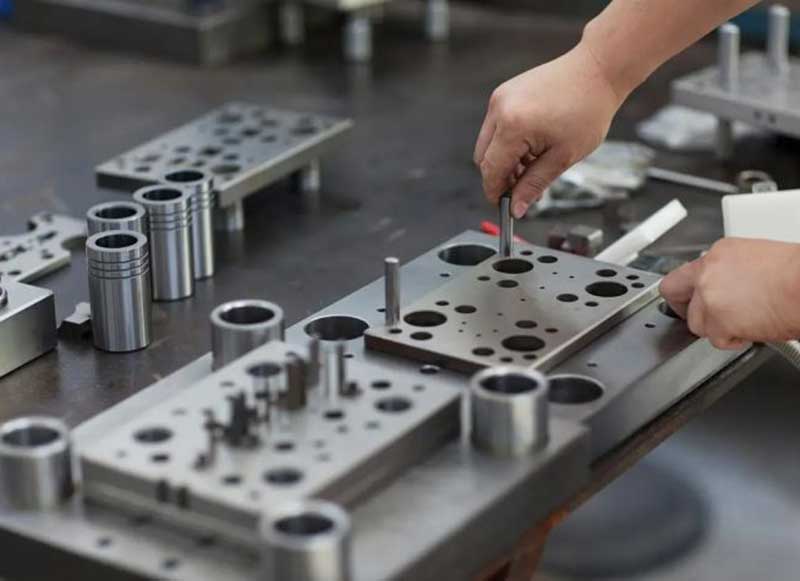
High-precision design and simulation technology
Leveraging CAD/CAE software such as SolidWorks and AutoForm, we conduct detailed 3D modeling and stamping simulations to detect potential deformation risks in advance — reducing trial-and-error costs by up to 20%. Our mould precision reaches ±0.01mm, ideal for micro-scale parts like electronic connectors and medical components.
Intelligent processing and molding technology
Our advanced equipment includes five-axis CNC machining centers for complex cavity processing (Ra≤0.8μm), CNC EDM machines from Sodick and Makino for deep and non-standard hole shaping, and high-accuracy wire cutting (±0.005mm) for cutting high-hardness materials — all ensuring exceptional mould precision and durability.
Efficient production system
We implement multi-station progressive dies to streamline punching, stretching, and forming in a continuous cycle, boosting production efficiency by over 30%. For flexible, small-batch, multi-variety needs, our compound die technology completes multiple forming processes in a single stroke, minimizing downtime and tooling changes.
Find High-Quality Metal Stamping Mould Services?
Partner with a trusted expert to reduce lead times and enhance your manufacturing efficiency. Get a free consultation today! Click below to inquire now and let’s create the perfect mould for your needs.
FAQs About Custom Metal Stamping Mould
Standard molds: Delivery time is 25-35 days (includes design, machining, and trial testing).
Complex molds (e.g., multi-station progressive dies): Requires 40-50 days.
Expedited service: Available upon request, with a minimum delivery time of 20 days (subject to process feasibility evaluation).
General recommendations:
High hardness: SKD11/DC53 alloy steel (lifespan >1.5 million cycles).
Corrosion resistance: SUS304 stainless steel (for medical/outdoor applications).
Lightweight: Aluminum alloy (aerospace/consumer electronics).
Value-added service: Material performance test reports and selection guidance provided.
Technical safeguards:
TD coating technology enhances wear resistance.
Regular blade maintenance and heat treatment.
Inspection standards: Full-process online inspection (2.5D CMM, cleanliness detector).
Trial services: Yes, we offer trial production for 100-500 units to optimize parameters before mass production.
Transparent pricing: Trial costs are quoted separately based on complexity and can be offset against bulk orders.
Key controls:
Dimensional accuracy: Full inspection via 2.5D CMM (tolerance ±0.03mm).
Surface quality: Cleanliness detectors ensure no oil stains or burrs.
Functional validation: Simulated real-world tests during trial phases (e.g., tensile strength, assembly compatibility).
Optimization technologies:
AI-powered nesting system achieves >90% material utilization.
Waste recycling in progressive dies (e.g., 15% material saved in battery shell production).
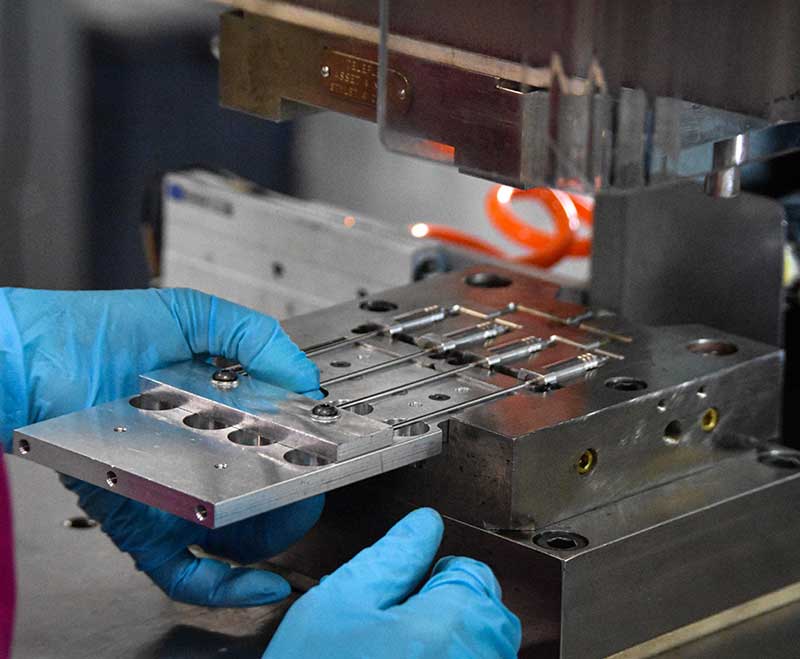
Get a Free Consultation Now
Ready to elevate your production efficiency with a trusted China stamping mould partner? Zhengqiang Group delivers precision-engineered moulds backed by advanced design, intelligent machining, and full-cycle support. Contact us today to get a customized solution tailored to your industry needs.